Plastic molding is a complicated process and there are several aspects that influence it deeply. One of these aspects is the type of material you use for your plastic molding process. If you want to ensure a seamless workflow where your plastic molding machines work as flawlessly as ever, it is crucial that you choose the perfect type of material for your plastic molding machine.
According to plasticmold.net, one of the leading OEM plastic manufacturers in China, it is imperative that you use the perfect type of material for your production line or otherwise it might result in lethal manufacturing accidents and a decreased efficiency for your plastic products. This can severely hamper your business’s productivity.
That is exactly why we are here to help you out. In this article, we will be listing several points why the selection of proper materials is extremely crucial in the plastic molding process and why it matters a lot to your business’s production line and work process.
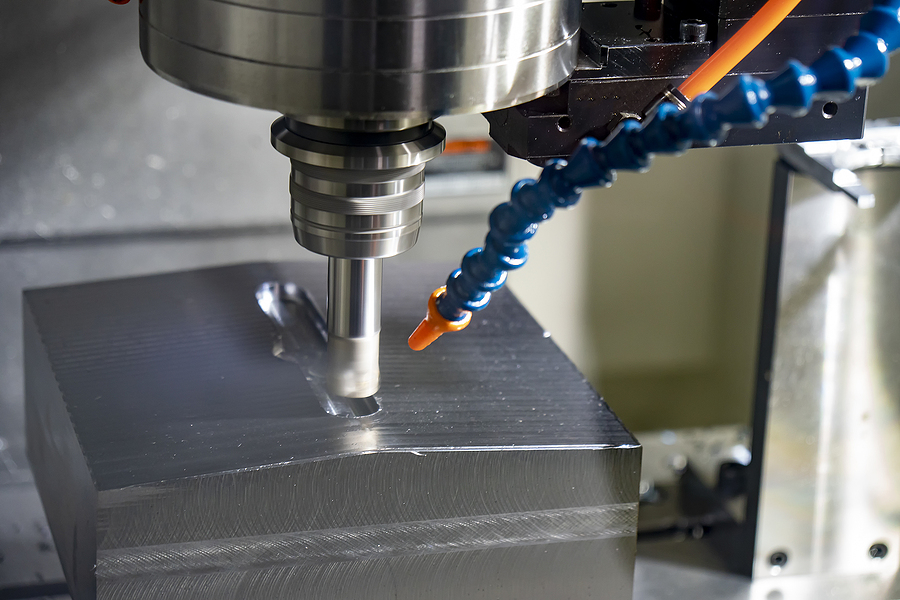
Why is material selection so important?
Material selection is one of the hardest factors in a plastic molding production process. Once you know the right type of material from the start, you can designate your other machines in the production line to be compatible with it.
Not fixing on a single chosen material beforehand can cost you several tool adjustments that can prove to be super expensive later in terms of machine errors and loss of precious time and productivity. It is necessary that you understand injection molds are specially made for a single type of material.
Diverting from this assigned material can result in serious machine and material compatibility. There are various factors that decide which material is optimal for which plastic mold and use. Making the right choice in this scenario is extremely important as it is responsible for your entire project’s success.
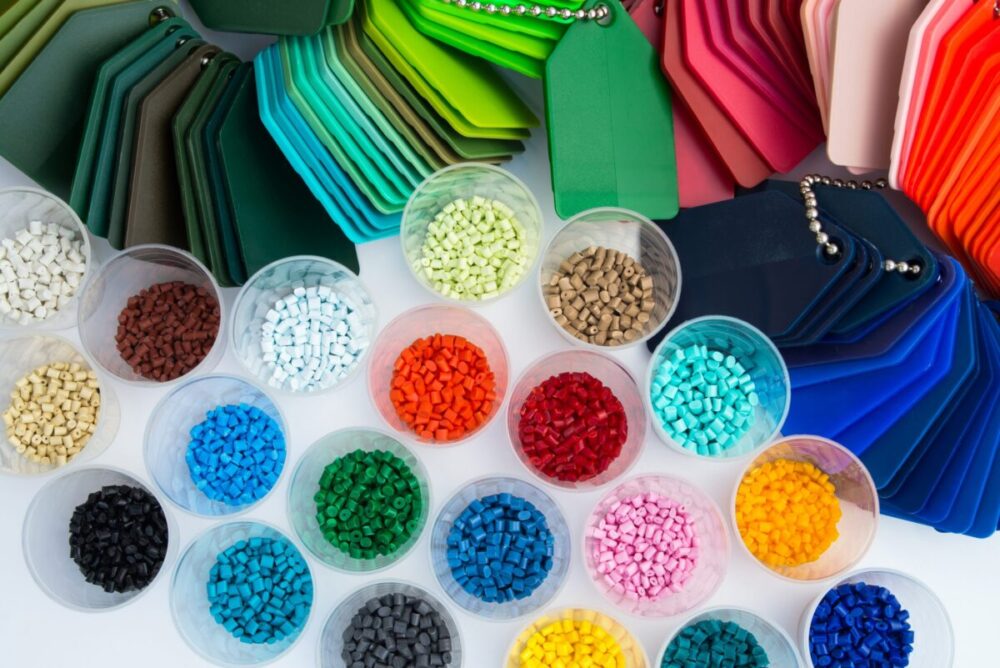
What aspects do you need to consider to choose the perfect material?
There are several aspects that come into play when choosing the perfect plastic molding material. These aspects are crucial because they dictate which material is best suited for a particular industry and can fulfill all the requirements of the business. These factors are:
- Durability – Durability is arguably one of the most important aspects of a plastic in the injection molding industry. How durable a plastic is defines how much pressure and force it can survive in harsh conditions. Additionally, durability also shows the plastic’s ability to withstand scratches and marks when undergoing the aesthetics improvement process. It also plays a vital role when you consider its importance in high accuracy applications. .
- Flexibility – Flexibility refers to the plastic material’s ability to bend and change its shape temporarily without breaking apart completely or going completely out of shape. A durable plastic can also be extremely flexible. The flexibility of the material dictates what use it will be best utilized in.
- Temperature resistance – All plastic can be melted at some point or the other, or alternatively made brittle with freezing cold – the question is how much can it endure before going out? If the material that you use doesn’t have a high temperature resistance, the injection molding process won’t be as effective. Also, the products will lose their integrity if they are used in high temperature environments. The same applies on the other scale where the colder a plastic gets, the more brittle it becomes.
- UV resistance – If you are designing a product that is going to be exposed to large amounts of sunlight, it is important that you check if the material has sufficient UV resistance to handle the plastic molding process. UV resistance indicates how much your product can retain its original properties when it is kept in harsh sunlight conditions for long amounts of time.
- Melting point and type – The temperature at which the solid plastic pellets used in the plastic molding process are melted to give them liquid form is called the melting point of that material. Additionally, it is important you note that not all plastic materials melt in the same manner. Some plastics melt gradually as their constitution reaches their melting point one by one. While on the other hand, some plastics melt altogether at the same time once their melting requirements have been satisfied.
- Viscosity – The viscosity, or thickness of a liquid, dictates how the plastic will flow once it is in liquid form. The less viscous the plastic is, the more freely it will flow
What are the different types of plastic used for plastic molding?
Now that you know all the different factors that are responsible for ensuring you obtain the right type of material for your use, we suggest you take a look at the most commonly used types of plastic and see what they are majorly used for:
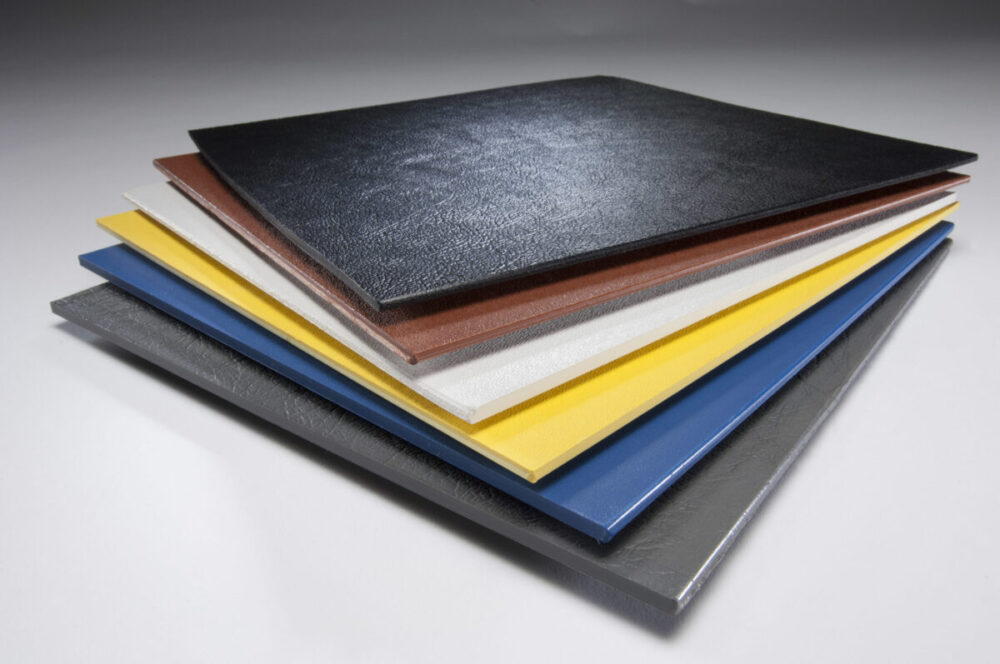
ABS Plastic
When it comes to the perfect standard material for plastic injection molding, it is none other than ABS Plastic. ABS Plastic is extensively used and is referred to as the most commonly used molding materials. It is extremely cheap and has amazing structural length.
Polyethylene
Next in line after ABS, the second number contender that runs as the most widely used type of plastic material is the Polyethylene material. The material is extremely versatile and multi-faceted and serves a number of purposes on this planet.
Polycarbonate
If you are looking for a material that can withstand high amounts of heat and is relatively transparent, your best bet will be going for a polycarbonate.
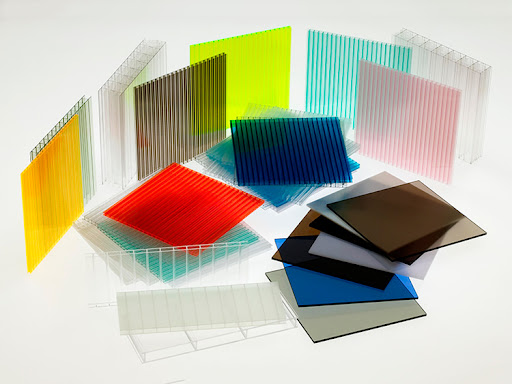
Ultem
Ultem is one of the higher end plastics that everyone loves and relies on. It is used in countless applications and it has amazing heat resistance. The strength it offers is off the charts and people have used them everywhere such as electronic, aerospace or headphones.
Polypropylene
Polypropylene is just like another plastic material. However, it does have one excellent point that makes them worth keeping around and manufacturing products in.
Acetal
Acetal has been serving as an alternative polymer to metal for quite some time now due to its shineness and brittleness.
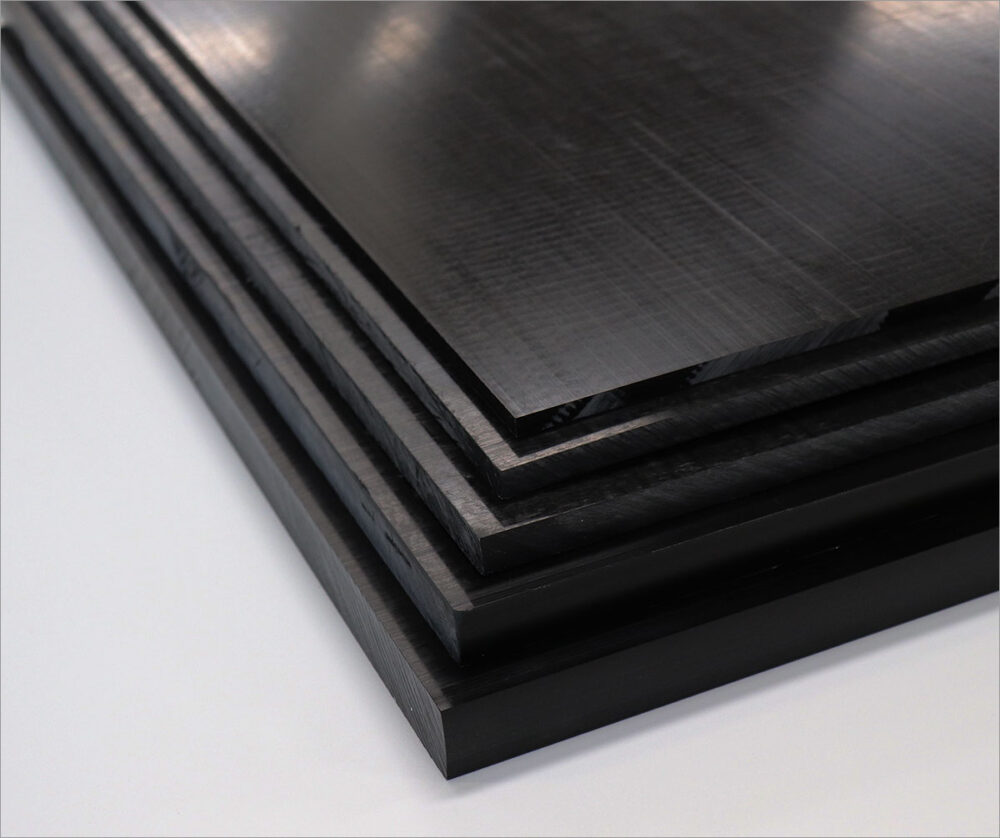
Nylon
Nylon is one of the most popular multipurpose polymers. If a component requires considerable amounts of strength from the polymer, nylon can deliver easily.
Conclusion
There are several reasons why material selection is extremely important in the plastic molding process. If the article was insightful for you, then please consider following our website for regular updates as it will help us out immensely.