Did you know that control cables play a crucial role in maintaining precision in various systems?
These seemingly simple components are responsible for ensuring the smooth and accurate operation of a wide range of machinery.
But what exactly makes control cables so important? How do they contribute to the overall performance and efficiency of different industries?
In this discussion, we will explore the significance of control cables, the types commonly used, and the factors that impact their performance. So, buckle up and get ready to discover the backbone of precision in systems.
The Role of Control Cables in Systems
Control cables play a crucial role in precision systems, serving as the backbone that enables efficient and accurate control of various functions and operations. The advantages of using control cables are numerous, making them an essential component in a wide range of industries.
One of the key advantages of control cables is their ability to transmit motion and force over long distances. Unlike other control mechanisms, such as hydraulic or pneumatic systems, control cables don’t require the use of fluids or gases. This makes them ideal for applications where the use of such mediums is impractical or inefficient.
Additionally, control cables offer precise control and feedback, allowing for accurate and responsive operation of systems. This is particularly important in industries such as aerospace, automotive, and robotics, where precise control is critical for safety and performance.
Control cables find applications in various industries, including transportation, manufacturing, and entertainment. In the transportation industry, control cables are used in vehicles to control functions such as throttle, brakes, and steering. In manufacturing, control cables are utilized in machinery to control operations such as cutting, lifting, and positioning. In the entertainment industry, control cables are employed in stage rigging systems to control lighting, sound, and scenery.
Types of Control Cables Used in Various Industries
With the understanding of the crucial role control cables play in precision systems, it’s now important to explore the various types of control cables used in different industries. Control cables are essential in transmitting mechanical forces, allowing for smooth and precise movement in a wide range of applications.
One common type of control cable is the push-pull cable, which is used in industries such as automotive, aerospace, and marine. These cables consist of a core wire surrounded by layers of protective sheathing, allowing for efficient transmission of force.
Another type is the Bowden cable, commonly used in bicycle gears and braking systems. Bowden cables have a flexible outer sheath and a solid inner wire, ensuring accurate and responsive control.
Advantages of control cables include their ability to transmit force over long distances, their flexibility, and their resistance to harsh environments. However, they do have some limitations. Control cables can experience wear and tear over time, leading to reduced performance and potential failure. Additionally, they may be prone to stretching or breaking under excessive force.
Common materials used in control cable manufacturing include stainless steel, galvanized steel, and nylon. Stainless steel cables offer high strength and corrosion resistance, making them suitable for demanding applications. Galvanized steel cables are cost-effective and provide good durability. Nylon cables are lightweight and flexible, making them ideal for applications where weight and flexibility are critical.
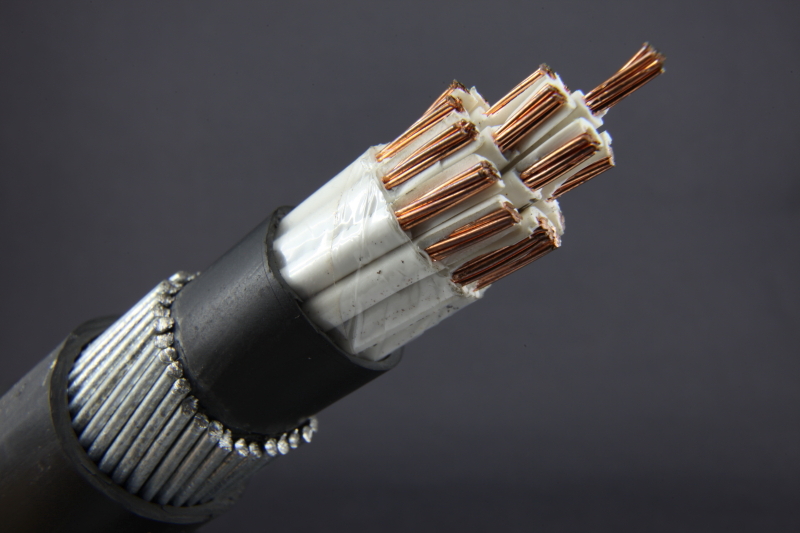
Importance of Precision in Control Cable Design
Precision in control cable design is of utmost importance to ensure optimal performance and reliability in various industrial applications. Control cables play a crucial role in manufacturing processes by providing the necessary communication and control between different components and systems. The advantages of precision control cable design are numerous.
Firstly, precise control cable design allows for accurate and efficient transmission of signals or power. By minimizing signal loss and interference, precision control cables ensure that the intended commands are accurately transmitted, resulting in improved control and operation of the system.
Secondly, precision control cable design minimizes the risk of cable failure. Control cables that are designed with precision are more resistant to wear and tear, reducing the chances of cable breakage or malfunction. This leads to increased reliability and longevity of the control cable, which is essential in industrial applications where downtime can be costly.
Furthermore, precision control cable design enables better integration and compatibility with other components and systems. By following industry standards and specifications, precision control cables can be easily installed and connected to different equipment, enhancing the overall performance and functionality of the system.
Factors Affecting the Performance of Control Cables
To ensure optimal performance and reliability of control cables, it’s crucial to understand the various factors that can impact their overall performance. One of the key factors that affect control cable performance is the environment in which they’re installed. Environmental conditions such as temperature, humidity, and exposure to chemicals can have a significant impact on the performance and lifespan of control cables.
Extreme temperatures can cause the cables to expand or contract, leading to loosening or tightening of connections and potential failure. High humidity levels can result in corrosion and degradation of the cable materials, affecting their electrical conductivity and mechanical strength. Exposure to chemicals, such as oils, solvents, or acids, can also lead to deterioration of the cable insulation and sheathing, compromising their performance and lifespan.
In addition to environmental factors, there are other factors that can affect the lifespan of control cables. These include mechanical stress, bending radius, and repetitive movement. Excessive mechanical stress, such as pulling or twisting, can cause the cables to stretch, deform, or break, affecting their electrical conductivity and integrity. Improper bending radius, which is the minimum radius at which a cable can be bent without causing damage, can also lead to cable failure. Repetitive movement, especially in applications with frequent flexing or vibration, can cause fatigue and wear on the cable, reducing its lifespan.
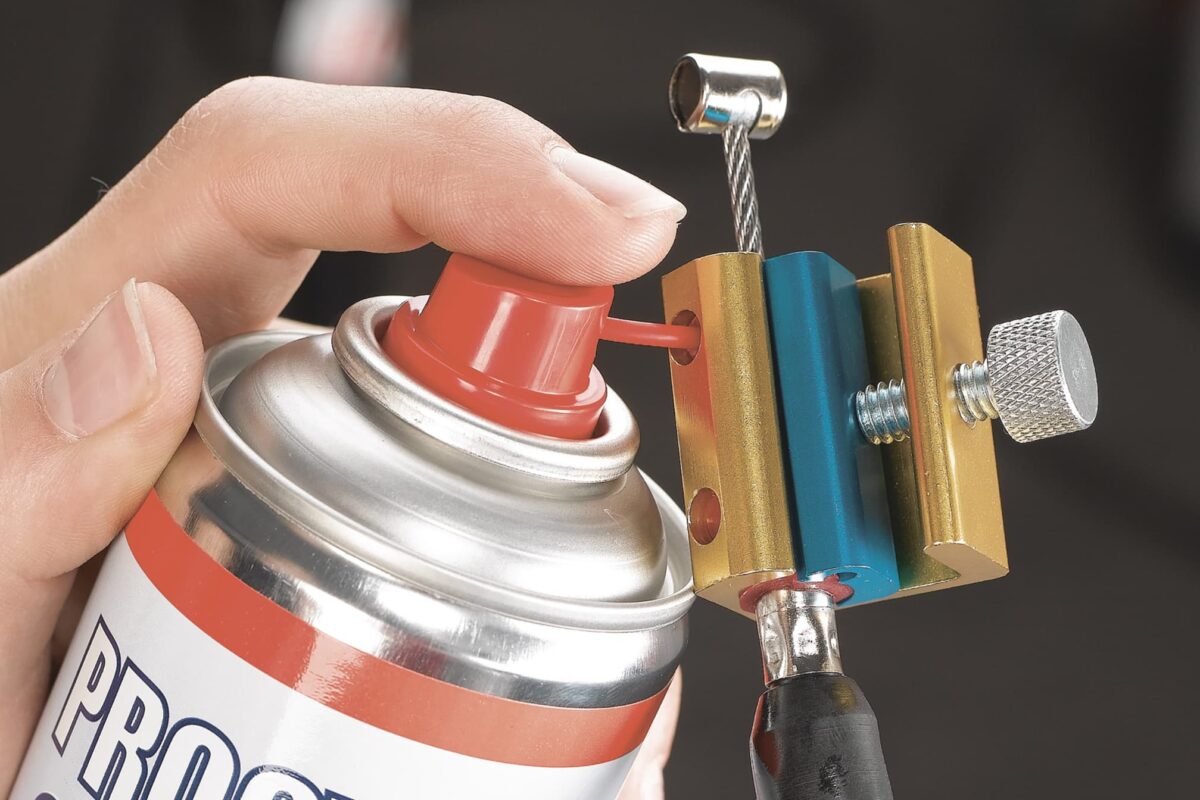
Maintenance and Troubleshooting of Control Cables
Regular maintenance and troubleshooting procedures are essential for ensuring the optimal performance and longevity of control cables. By implementing proper maintenance techniques, you can identify and address common issues promptly, preventing costly downtime and potential system failures.
To effectively maintain control cables, start by conducting regular visual inspections. Look for signs of wear, such as fraying or kinking, and check for any loose connections. Additionally, ensure that the cables are correctly aligned and properly lubricated. By addressing these issues early on, you can prevent further damage and extend the lifespan of your control cables.
Another crucial maintenance technique is to regularly test the cables for continuity and signal integrity. This can be done using specialized testing equipment that measures resistance, capacitance, and insulation resistance. By performing these tests, you can identify any potential faults or breaks in the cables, allowing for timely repairs or replacements.
Common issues that may arise with control cables include cable degradation, signal interference, and improper grounding. Cable degradation can occur due to factors such as environmental conditions, excessive bending, or improper storage. Signal interference can result from electromagnetic interference or poor cable shielding. Improper grounding can lead to signal distortion or electrical hazards.
Frequently Asked Questions
What Are the Common Materials Used in the Construction of Control Cables?
The common materials used in control cables include stainless steel, galvanized steel, and nylon. These materials possess desirable properties such as strength, flexibility, and corrosion resistance. They find applications in various industries, including the automotive sector.
How Do Control Cables Differ From Other Types of Cables Used in Systems?
You may be surprised to learn that control cables differ from other types of cables used in systems. They offer numerous advantages and have a wide range of applications. Let’s delve into the details.
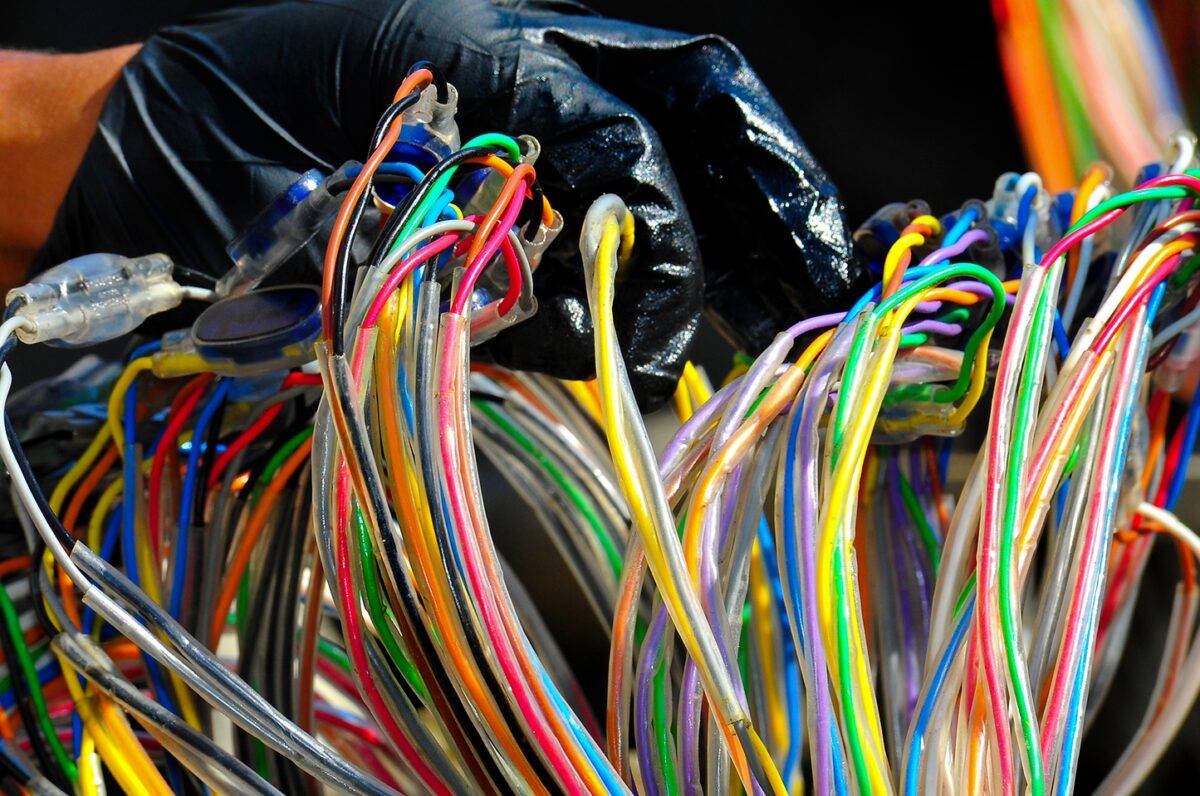
Are Control Cables Suitable for Use in Extreme Environmental Conditions?
Control cables are suitable for extreme environmental conditions as they are designed to withstand high temperatures and harsh weather. Ensure reliability and longevity by maintaining control cables regularly in such environments.
What Are the Potential Risks or Failures That Can Occur With Control Cables?
You may encounter potential risks or failures with control cables, such as electrical interference and mechanical fatigue. These issues can disrupt the precision and performance of systems, leading to malfunctions or breakdowns.
Can Control Cables Be Customized or Modified to Meet Specific System Requirements?
Yes, control cables can be customized or modified to meet specific system requirements. This allows for greater flexibility and precision in system operations. The benefits of using customized control cables include improved performance, reliability, and efficiency.