Welcome to the vibrant world of lawn grass manufacturing, where both natural and artificial turf come to life. This article will specifically delve into the intricate process of artificial turf manufacturing, shedding light on how synthetic grass is crafted, along with essential points to consider for both purchasing and installation.
The turf industry has witnessed remarkable advancements, offering innovative low-maintenance solutions for homeowners and sports facilities alike.
The Turf Production Process
The Turf Production Process involves several distinct stages, each essential to producing high-quality artificial grass. Understanding these stages provides insight into how various materials contribute to the final product’s performance and durability.
Stages of Artificial Turf Manufacturing
The process begins with the extrusion stage, where nylon, polypropylene, or polyethylene pellets are melted and mixed with specific additives. This stage forms the yarn into durable strands, ensuring impressive aesthetics and strength.
Following extrusion, the tufting stage takes place, in which the yarn is sewn into a backing material, mimicking the layout of natural grass. The final stages include drying, coating, and quality control checks. It is during these checks that manufacturers ensure the artificial grass meets stringent standards set for quality control.
Materials Used in Turf Manufacturing
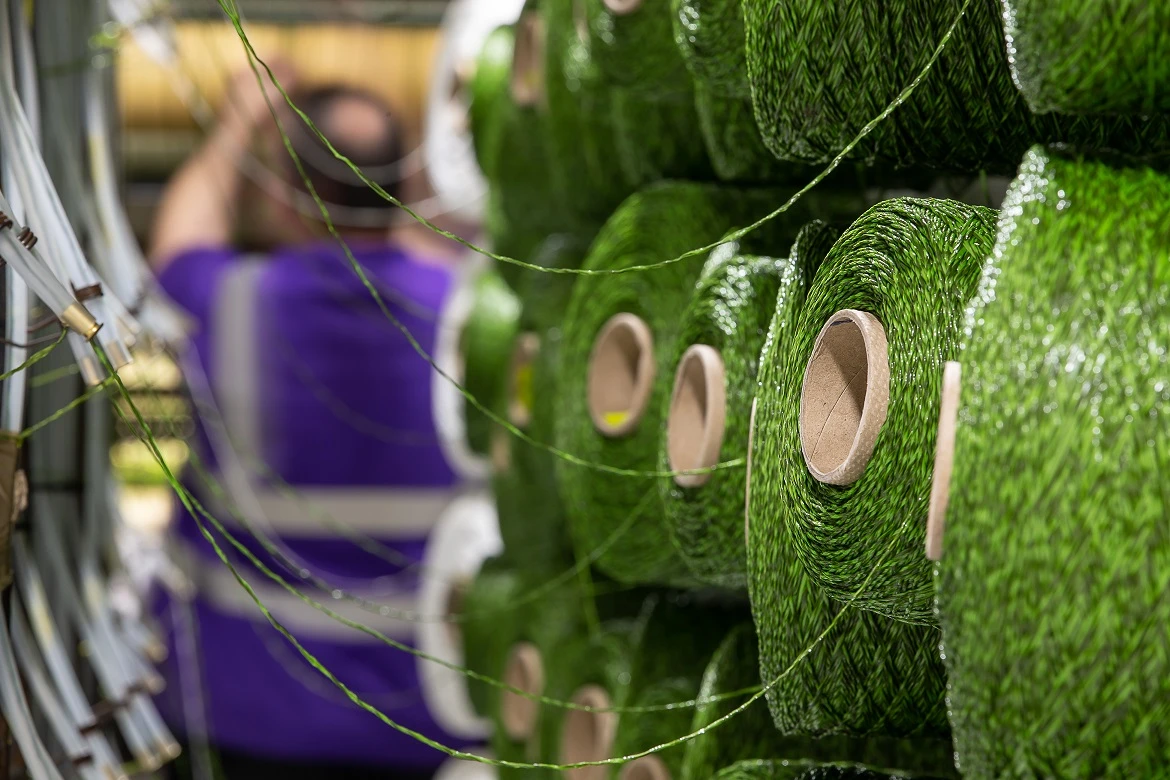
The choice of materials critically impacts artificial turf quality and performance. Nylon is famous for its strength and resilience but can be stiffer and more costly. Polypropylene is often utilized for the thatch layer, softening the overall feel while enhancing aesthetics.
Polyethylene has become the preferred material due to its excellent balance of durability and softness, making it suitable for both residential and sports applications. Innovations, such as fibrillated and monofilament yarns, have enhanced the visual appeal and overall performance of the turf, allowing consumers to choose options that best suit their needs.
Importance of Yarn Fiber Quality
Yarn fiber quality serves as a cornerstone for the functionality and longevity of artificial turf. Different fiber types yield various textures and appearances, with high-quality yarn fibers ensuring superior resilience against heavy foot traffic and color fading.
Advances in technology, like the introduction of C8, provide a purer, stronger polymer specifically for high-end turf products. To further enhance durability, manufacturers incorporate UV inhibitors and color additives during the extrusion process, resulting in durable turf solutions that blend both beauty and functionality.
Material Type | Characteristics | Applications |
Nylon | Strong, durable, costly | High-traffic areas |
Polypropylene | Soft, enhances aesthetics | Thatch layers, less demanding applications |
Polyethylene | Durable and soft, cost-effective | Residential lawns, sports fields |
Lawn Grass Manufacturing – How Turf is Made and What You Need to Know
Understanding the processes used in artificial turf production is essential for anyone interested in this innovative field. Two significant techniques dominate the turf manufacturing landscape: extrusion and tufting. Each method plays a critical role in determining the quality and performance of the final product.
Understanding Extrusion and Tufting Techniques
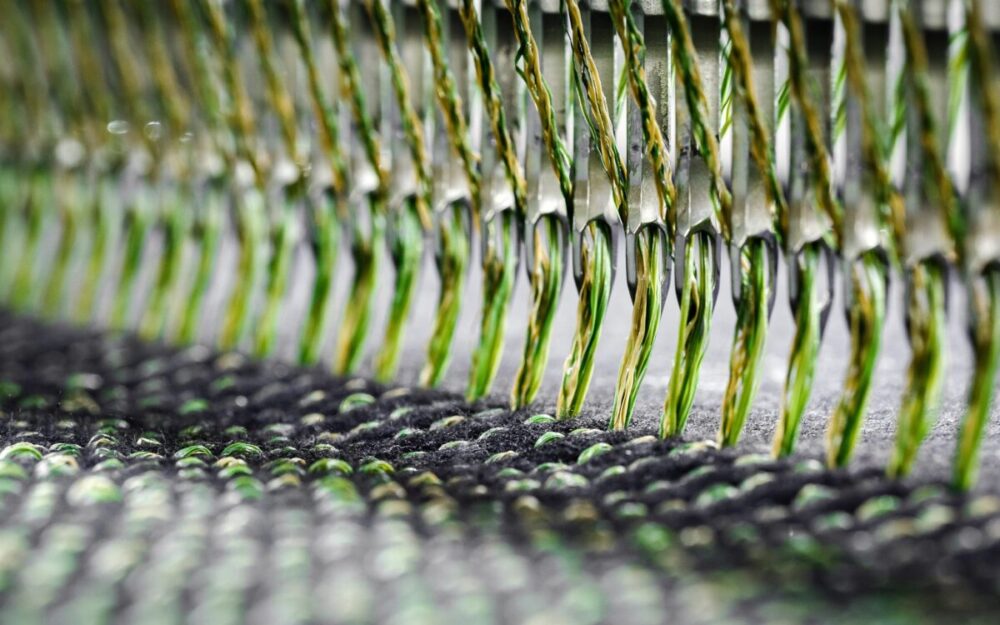
Extrusion techniques involve melting raw polymer pellets mixed with additives to create durable strands of fiber. These fibers are initially brittle but become resilient once cooled. After this initial processing, the fibers are transformed into yarn, which serves as the foundation of artificial turf.
Secondary Backing and its Role in Durability
The incorporation of secondary backing is a pivotal step in turf manufacturing, significantly enhancing durability and turf stability. Typically composed of latex or polyurethane, this backing is applied after tufting. Its primary function is to secure the tufted fibers tightly, creating a fortified structure resistant to wear and tear.
Applying secondary backing involves a heating and curing process, ensuring a robust bond forms between the backing and the fibers. Furthermore, drainage holes are often integrated into the backing to promote a healthy environment for the turf.
This additional layer becomes increasingly important for high-traffic areas, serving as a fundamental aspect to consider when selecting the ideal turf for your needs. For more details on the manufacturing process and material specifications, you can explore resources from experienced suppliers.
Conclusion
In summary, understanding the intricacies of lawn grass manufacturing and the processes involved in how turf is made is crucial for anyone contemplating the use of artificial grass in their residential or commercial spaces. This knowledge not only encompasses the production stages but also highlights the importance of selecting high-quality materials that impact your lawn’s long-term performance.