Increasing gross earnings and retaining competitiveness require ongoing productivity development, regardless of the size of your company. On the machine shop floor, productivity is determined by a combination of efficient personnel, equipment, and processes. In all of these areas, continuous improvement entails assessing present processes and making improvements to systems, personnel training, and even the equipment used to produce parts and components.
However, some problems aren’t as obvious, such as when there’s too much going on at the same time, and the complexity slows down your entire operation. You’ll improve your capacity to spot problems and solve them as you develop the practice of looking for ways to boost manufacturing productivity.
1. Examine your workflow
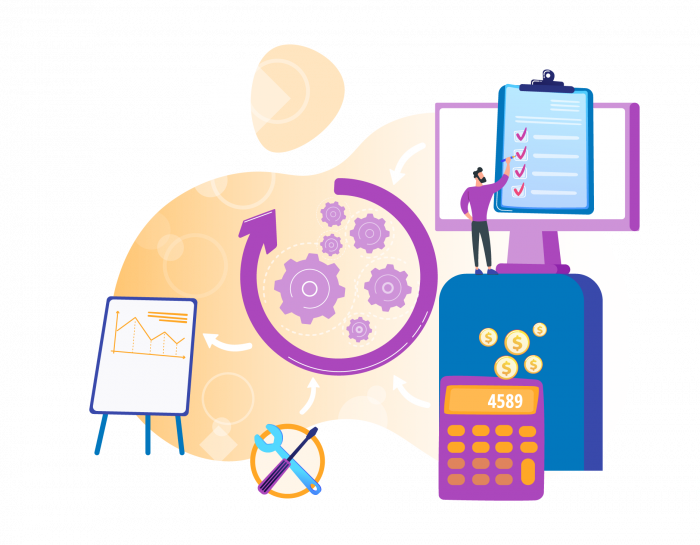
If you’re looking for ways to boost manufacturing efficiency, the best place to start is by identifying which elements of your workflow are inefficient. Examining the processes in your manufacturing company necessitates taking into account a number of aspects, including the staff, the hardware they utilize, and the physical action of production.
Other factors to consider include the level of communication in the workplace, the diversity of resources required to execute activities (raw materials, electricity, and so on), and so on.
2. Train and incentivize employees
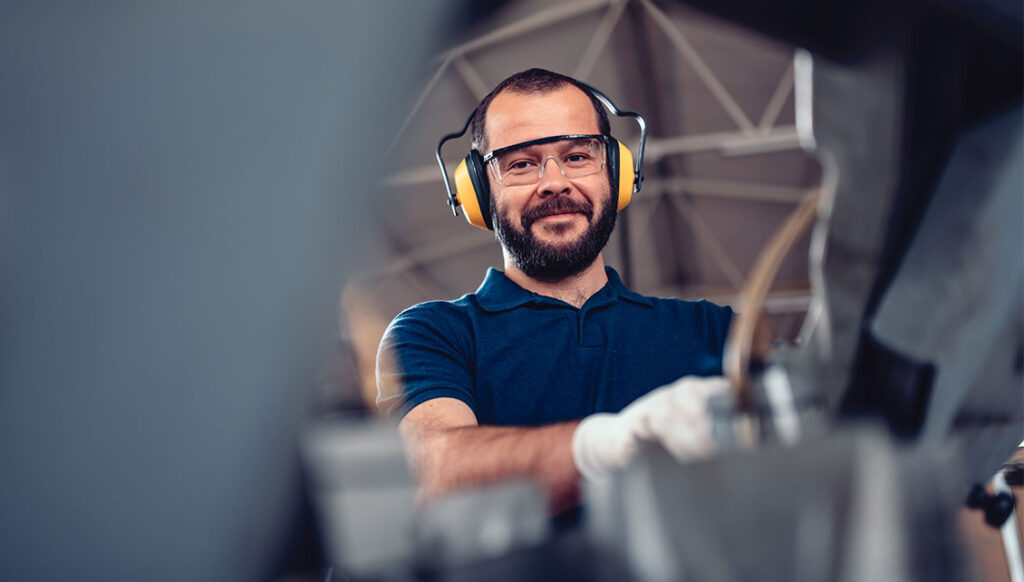
Training employees is one of the most usually neglected techniques to boost industrial production.
Depending on your sector and product type, your equipment and procedures are likely to change in some way on a regular basis. New product lines, technology developments, and even regulatory changes could all be factors.
As a result, training employees – even those who have been with you for a long time – can lead to better adherence to best practices and, as a result, increased productivity.
Cross-training is another overlooked factor. Having multi-skilled employees guarantees that productivity does not suffer when team members are absent (due to illness, planned absence, or holidays).
Integrate technology with your manufacturing productivity process. Visit ezfactory.nl to know more.
3. Understand the product(s) that are being manufactured
Knowing the items that you are making might produce surprising results, similar to teaching workers on how to run different machines or different processes throughout your manufacturing setup.
Manufacturing productivity starts with trained workers who feel engaged and valued (a side effect of training), with the added benefit that it can often lead to employee-generated ideas for improvement.
This doesn’t have to be in a conventional classroom setting. Supervised on-the-job training can be just as beneficial while being less distracting.
4. Make a list of all the materials and pieces you’ll need (efficient retrieval)
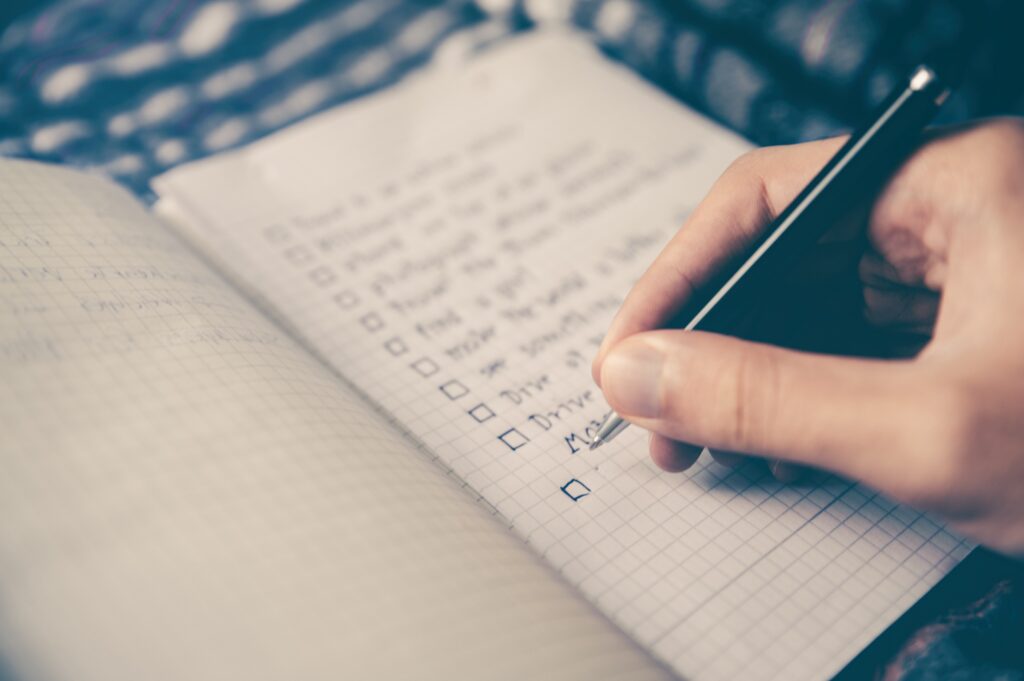
The amount of money (and staff time) wasted due to a lack of organization can be enormous.
This is especially true if materials or components are held at different stages of the manufacturing process, with time spent obtaining these items accounting for a large chunk of your (staff) costs.
Having well-organized storage and warehousing facilities will help with this “picking” process, which can be further improved with the use of appropriate parts or picking bins.
Revisit every step of your supply chain process, the faster the parts or components arrive at your manufacturing line, the more productive you will be. It will also help you avoid delays and production halts while you wait for items. Make sure you have a high-quality software that can help you through this process; visit here: https://www.etq.com/supply-
5. Reduce waste
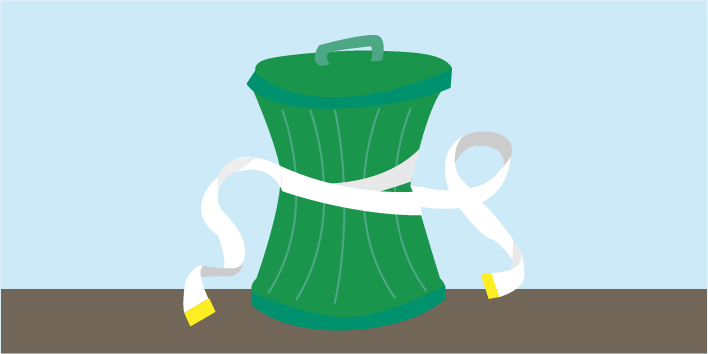
Every component that is broken and cannot be used is a financial drain. It costs money to have an unfinished product. Every item returned by a customer costs you money and tarnishes your brand and reputation.
As a result, it’s critical to keep objects safe while they’re being stored (in picking bins) or relocated (handling totes).
While it’s understandable that mistakes happen, if they happen too frequently, getting to the root of the problem and figuring out a solution (either through training/recruitment, new processes, or new equipment, for example) is vital.
6. Cut down on downtime
A majority of the preceding points are directly tied to minimizing manufacturing downtime. Several factors can lead to the occurrence of downtime. However, it can be avoided.
Failure to maintain machines, for example, might result in malfunctions that block production lines.
When employees pick the wrong components (perhaps due to a deficient organization), production can be hampered. Similarly, if components do not arrive on time on the production line, this can cause delays.
A highly flexible multi-skilled workforce is required to work in different areas of your factory to help cope with bottlenecks or to deal with scheduled or unforeseen absences in certain areas if needed.
It is crucial to remember that you are eventually losing money every minute of delayed manufacturing.
7. Get ready for the unforeseen
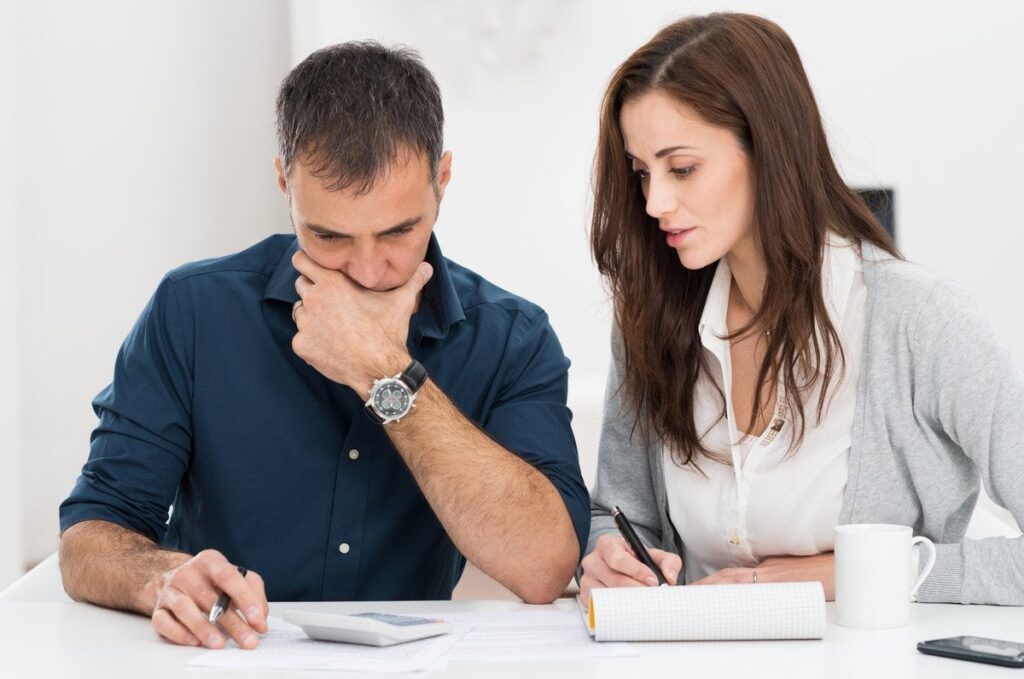
Finally, it can be crucial for productivity levels to be ready for demand peaks.
While higher productivity definitely helps to overcome any problems given by increased workload (that can be seasonal, due to unforeseen product success, or an enormous array of external circumstances beyond your control), lack of preparation can also prevent productivity.
When a product backlog develops, it can lead to demotivation among employees. Again, efficient processes and multi-qualified personnel are crucial to ensure an organization’s productivity with the necessary equipment.
Conclusion
The process of boosting productivity does not have a one-size-fits-all answer, and it cannot be enhanced with a single modification. Increasing your productivity is a constant process that involves conscious and continuing modifications in various areas, as mentioned above.
Expecting people to commit more energy and time in order to boost output is inefficient and ineffective, and it raises a number of ethical and safety concerns. A number of areas for improvement can be uncovered by comprehensively mapping the workflow operations within a manufacturing facility.
Small modifications applied in different processes can result in significant increases in total production. Simple adjustments like workplace organization, equipment upkeep, and employee training are inexpensive and easy ways to increase productivity and create a harmonious work atmosphere.