The Benefits of Using Push Back Racking Systems in Your Warehouse
Push back racking systems are a popular choice for warehouse storage due to their numerous benefits. These systems offer an efficient and space-saving solution that can greatly enhance the productivity and organization of your warehouse operations. Here are some of the key benefits of using push back racking systems:
- Increased storage capacity: Push back racking systems maximize the use of vertical space in your warehouse, allowing you to store more products in a smaller footprint. By utilizing the depth of the racking system, you can store multiple pallets deep, which significantly increases your storage capacity.
- Easy accessibility: Unlike traditional pallet racking systems, push back racks operate on a last-in, first-out (LIFO) principle. This means that the pallets that are loaded last will be the first ones to be unloaded, ensuring easy access to your inventory. This feature is especially beneficial for warehouses with high stock turnover or time-sensitive products.
- Improved picking efficiency: With push back racking systems, items are stored in a way that allows for efficient stock rotation. As new pallets are loaded onto the system, the existing ones are automatically pushed towards the aisle for easy retrieval. This rotation system saves time and effort during order picking, resulting in improved overall efficiency.
- Enhanced safety: Push back racking systems are designed with safety in mind. The sturdy construction and built-in safety features such as safety stops and locking mechanisms ensure that pallets remain securely in place during loading and unloading processes. This reduces the risk of accidents or damage to both personnel and inventory.
- Versatility and adaptability: Push back racking systems can be customized to fit your specific warehouse requirements. They can accommodate various pallet sizes and weights, making them suitable for a wide range of industries and products. Additionally, these systems can be easily reconfigured or expanded as your storage needs evolve over time.
- Cost-effective solution: By maximizing your warehouse space and optimizing storage capacity, push back racking systems can help minimize the need for additional storage facilities or warehouse expansions. This can result in significant cost savings for your business in the long run.
In conclusion, push back racking systems offer a range of benefits for warehouse operations. From increased storage capacity and improved accessibility to enhanced safety and cost-effectiveness, these systems can greatly optimize your warehouse space and streamline your inventory management processes. Consider implementing push back racking systems to reap these advantages and enhance the overall efficiency of your warehouse.
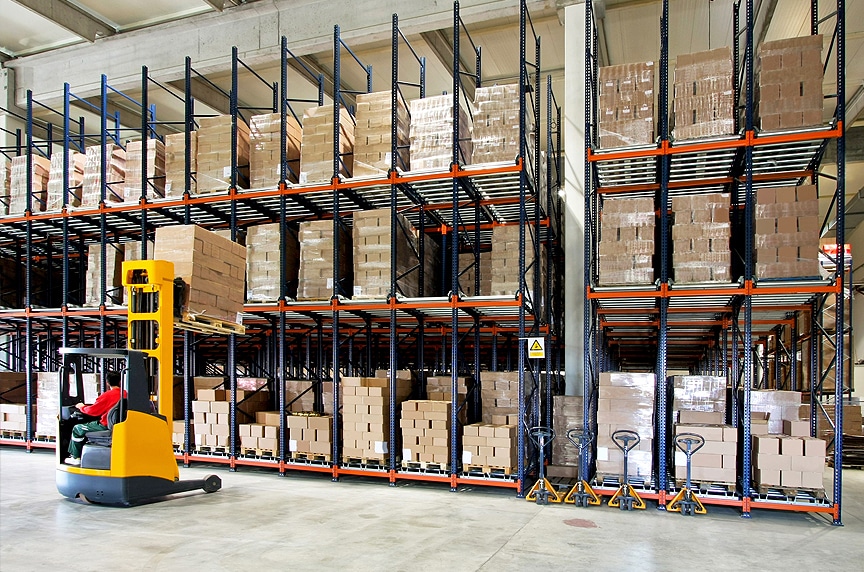
Key Factors to Consider When Determining Push Back Racking Dimensions
When determining push back racking dimensions, there are several key factors to consider. These factors will help ensure that the racking system is optimized for your specific needs and requirements. Here are some important considerations:
- Load capacity: It is crucial to determine the maximum load capacity of the push back racking system. This will depend on the weight and size of the products you plan to store. Be sure to account for any potential future changes in your inventory.
- Pallet size: Consider the dimensions of the pallets you will be using in your storage system. Push back racking is designed to accommodate specific pallet sizes, so it is important to choose a system that can effectively handle your pallet dimensions.
- Storage density: Determine how densely you want to store your products. Push back racking allows for high-density storage by utilizing a last-in, first-out (LIFO) system. This means that each lane can hold multiple pallets, stacked one behind the other. Consider the number of pallets you want to store per lane and calculate the required depth accordingly.
- Aisle width: The width of your aisles will depend on the type of material handling equipment you plan to use, such as forklifts or reach trucks. Ensure that your chosen push back racking system can accommodate the necessary aisle width for safe and efficient operations.
- Ceiling height: Take into account the height of your facility’s ceiling when determining push back racking dimensions. You want to make sure that there is enough vertical space to accommodate the height of the racking system, including any additional clearance required for material handling equipment.
- Accessibility: Consider how easily you need to access your products. Push back racking allows for easy access to multiple pallets within each lane, but keep in mind that retrieving pallets from deeper positions may require more time and effort.
- Safety considerations: Safety should always be a priority when selecting racking dimensions. Ensure that the system is designed to meet all safety standards and regulations, and consider factors such as load distribution, stability, and proper anchoring.
By carefully considering these key factors, you can determine the most appropriate push back racking dimensions for your specific storage needs. It is also recommended to consult with a professional racking supplier or engineer to ensure that your chosen system meets all necessary requirements.
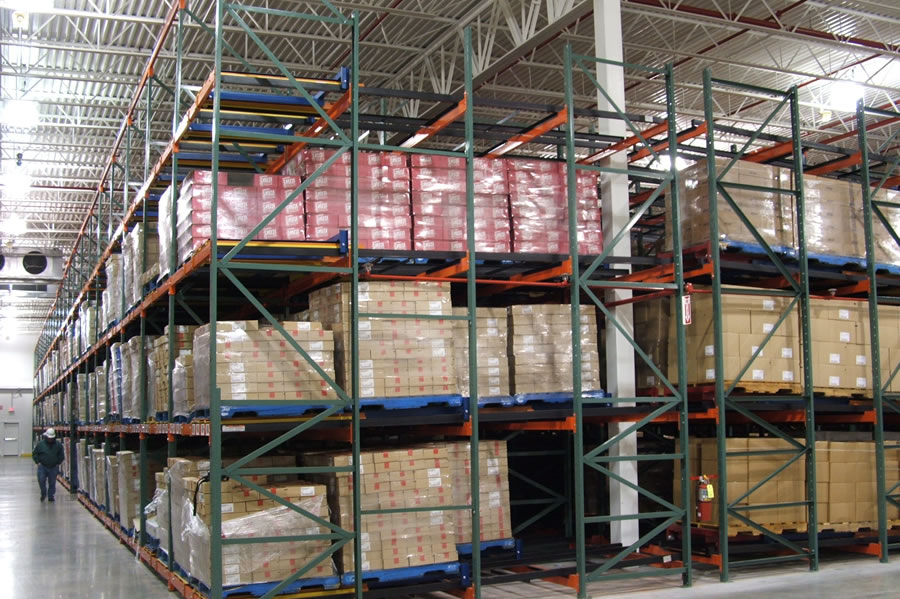
Tips and Tricks for Optimizing Push Back Racking Layouts Like a Tetris Pro
Optimizing push back racking layouts can indeed be compared to playing the game of Tetris. Here are some tips and tricks to help you optimize your push back racking layouts like a pro:
- Understand your inventory: Before you start arranging your push back racking, it’s crucial to have a clear understanding of your inventory. Analyze the dimensions, weight, and storage requirements of each item.
- Plan for accessibility: Consider the frequency of item retrieval when designing your layout. Place frequently accessed items near the front of the racking system for easy accessibility.
- Utilize vertical space: Push back racking systems allow for efficient use of vertical space. Take advantage of this by stacking items vertically whenever possible. However, ensure that weight limits and safety regulations are adhered to.
- Optimize slot depths: Adjusting the depth of each push back lane can be an effective way to maximize storage space. Analyze your inventory’s size and adjust the slot depths accordingly to achieve optimal utilization.
- Implement first-in, last-out (FILO) strategy: Push back racking systems generally follow a FILO retrieval method, where the last item loaded is the first to be picked. Organize your inventory accordingly, placing items with longer shelf life towards the back and those with shorter shelf life towards the front.
- Utilize software tools: There are various software tools available that can help you simulate and optimize your push back racking layouts. These tools can calculate load capacities, recommend slot depths, and provide visual representations of your optimized layout.
- Consider weight distribution: Ensure that the weight distribution within each lane is balanced to maintain stability and prevent any safety hazards. Distribute heavier items evenly across lanes and avoid overloading any single lane.
- Conduct regular maintenance: Regularly inspect and maintain your push back racking system to ensure its integrity and safety. Keep an eye out for any damaged components, such as rails or wheels, and replace them promptly.
Remember, optimizing push back racking layouts requires careful planning and consideration of various factors. By implementing these tips and tricks, you can optimize your layout like a pro and maximize your storage space efficiency.
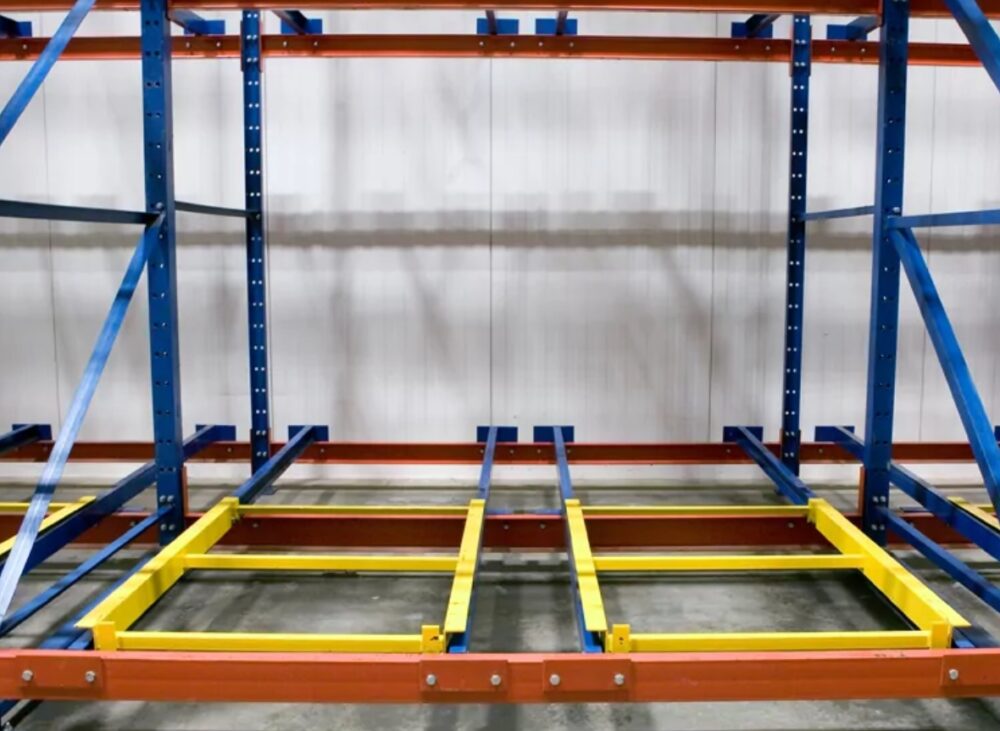
The Role of Technology in Determining and Managing Push Back Racking Dimensions
Technology plays a crucial role in determining and managing push back racking dimensions. Push back racking systems are designed to optimize storage space by allowing multiple pallets to be stored in a single lane, with each pallet pushed back as the next one is loaded. The dimensions of push back racking, including the height, width, and depth, need to be carefully calculated to ensure efficient and safe storage.
One way technology helps in determining push back racking dimensions is through advanced software and modeling tools. These tools take into account various factors such as the size and weight of the pallets, the type of goods being stored, and the available space. By inputting this information into the software, it can generate optimal dimensions for the push back racking system that maximize storage capacity while maintaining safety standards.
Additionally, technology can assist in managing push back racking dimensions by providing real-time monitoring and data analysis. Sensors can be installed on the racks to monitor factors such as load weight, stability, and rack utilization. This data can then be analyzed to identify any potential issues or inefficiencies in the dimensions of the system.
By leveraging technology in determining and managing push back racking dimensions, businesses can ensure that their storage systems are optimized for space utilization, safety, and efficiency. This ultimately leads to increased productivity, reduced costs, and improved overall warehouse operations.
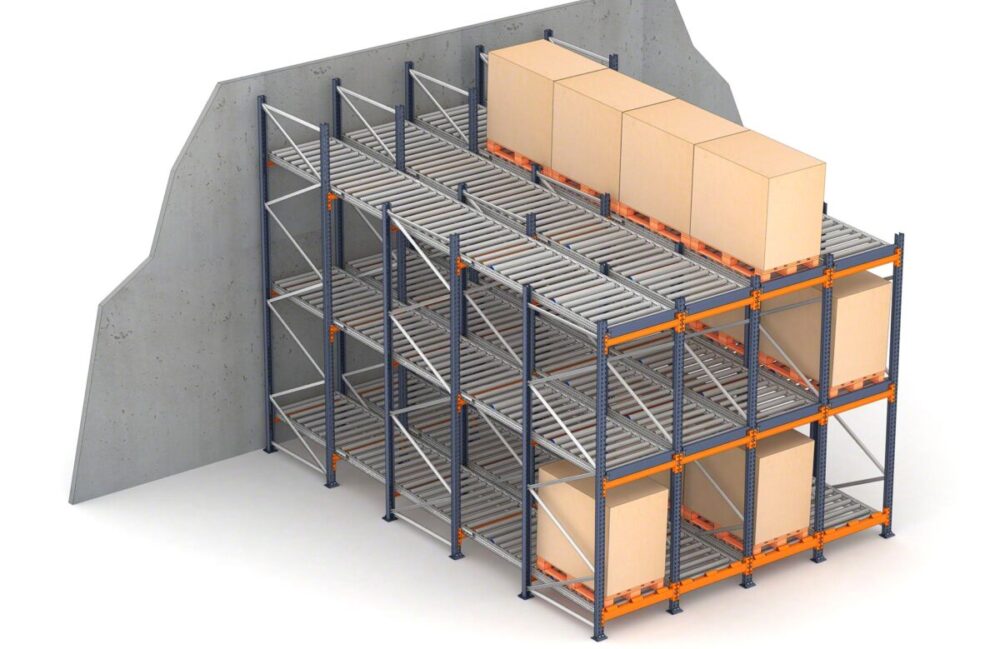
Conclusion: Mastering Push Back Racking Dimensions for an Organized and Efficient Warehouse Operation
Mastering push-back racking dimensions unlocks a well-organized warehouse with optimized storage, easy access, and streamlined inventory management. Understanding height, width, and depth ensures efficient layout for faster fulfillment and lower costs, while also empowering precise inventory tracking and replenishment. Ultimately, mastering dimensions turns push-back racking into a strategic tool for a thriving warehouse operation.